鹿島建設は、CO2を吸収して固まるコンクリート「CO2-SUICOM」の技術を応用し、2025年の大阪・関西万博の会場に延床面積263.99平方メートルの「CUCO-SUICOMドーム」を建設する。CO2を吸収するコンクリートとはどのような技術なのか。ドーム建設に至ったきっかけや研究開発の道のりを聞いた。文=萩原梨湖(雑誌『経済界』2024年8月号巻頭特集「歴史が動いた! 企業の素材発掘記」より)
CO2排出量が多い建設業で変化を遂げるコンクリート
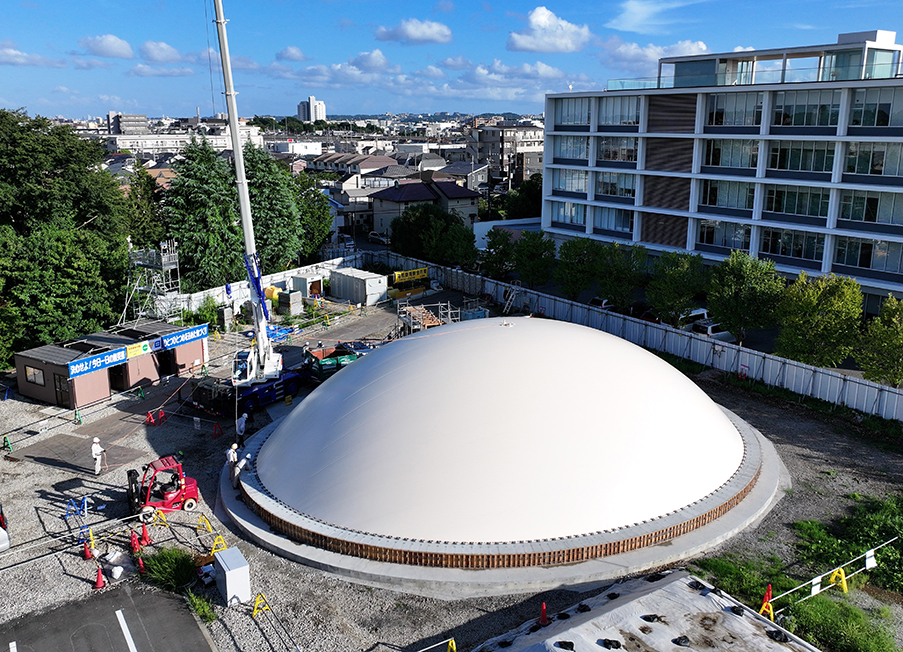
「CO2-SUICOM」(以下SUICOM)とは、2008年に鹿島建設が中国電力、デンカ、ランデスの3社と共同で開発した環境配慮型コンクリートだ。コンクリートが固まる過程でCO2を吸い込みコンクリート内部に固定することで、製造時に発生する以上のCO2を吸収することができる。
建設業は大量の建設資材を消費し、中でもコンクリート製造に関わるCO2排出量が多く、その削減が求められている。コンクリートはセメント、水、砂利・砂を混ぜて作られる。CO2を大量に排出するのは、原料の約10%にあたるセメントの製造過程だ。セメントは石灰石(CaCO3)を約1450℃で焼いて作るが、高温にする段階で大きなエネルギーを消費するとともにCO2を排出する。さらに、石灰石がセメントの主成分である酸化カルシウム(CaO)に変化する段階で石灰石から分離されたCO2が排出される。
通常のコンクリートは、セメントと水が反応することで固まるが、SUICOMはCO2を吸収することで固まる。SUICOMは、セメントの一部を「ガンマC2S」というCO2を吸収するカルシウム系の鉱物を含んだ素材に置き換えることで、セメントの使用量を減らしつつCO2を吸収することを実現した。
CO2を十分に吸収するまで長時間かかるため、建設現場での加工は現状ではハードルが高く、あらかじめコンクリート部材(プレキャストコンクリート)に加工しておく必要があった。高濃度CO2を充満させた養生室内で10センチ角ほどのブロックに成形し、歩車道の境界ブロックや舗装コンクリートブロックなどとして使用するのがこれまでの活用方法だった。
これだけでは用途が限定的なのでさまざまな建造物に展開するべく、21年度から、NEDO(国立研究開発法人新エネルギー・産業技術総合開発機構)のグリーンイノベーション(GI)基金事業「CO2を用いたコンクリート等製造技術開発プロジェクト」※が始まった。そこで、CO2を吸収させるドーム型の構造物「CUCO-SUICOMドーム(クーコスイコムドーム)」を建設する方針が決まった。建設方法は北米由来の「KTドーム」工法が採択された。手順は、強度の高いポリ塩化ビニール製のドーム膜に空気を送り込んで膨らませ、これを型枠として内側からコンクリートを吹き付ける。この時吹き付けるコンクリートの一部にスイコムを使用し、内側をCO2で充満させ固めることでドーム型の構造物が完成する。
23年に技術研究所(東京都調布市)の隣接敷地で「CUCO-SUICOMドーム」を建設、これが万博ドームの試験施工となった。
完成したCUCO-SUICOMドームは、SUICOMから3つの進化を遂げている。1つ目は、建物の耐久性・耐震性を保つ鉄筋コンクリートの部材に初めてSUICOMが使われたことだ。
「SUICOMの吹き付け時に鉄筋をきれいに巻き込まなければ鉄筋コンクリートとして成立しません。そのため北米の資格制度を導入し、作業員に高度な技術を身に付けてもらいました」(鹿島建設・閑田徹志氏)
2つ目は、あらかじめブロック状に製造しておくプレキャストコンクリートとは異なり、現場で直接作業ができるようになった点だ。3つ目は、これまで同社が環境配慮型コンクリートで作った構造物の中で最高クラスのCO2削減率を実現したことだ。CUCO-SUICOMドームでは、SUICOMだけで建設するとCO2吸収時間が長く工期が伸びてしまうため、内側の表面33ミリメートル部分にSUICOMを使っている。そのほかは、鉄鋼メーカーの副産物である高炉スラグ7割、セメント3割でできたECMというCO2排出量の少ないコンクリートを用いている。両者を掛け合わせることで従来の吹付コンクリートと比較し、材料由来のCO2排出量を70%削減することができた。
2つの課題をクリアしハイエンドの技術として活用
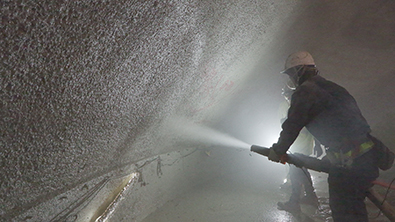
近年建設業各社は、環境配慮型コンクリートの開発を積極的に進めており、主に2通りの方法を組み合わせてCO2排出量を削減してきた。1つ目は、セメントを副産物で置き換える方法だ。この副産物の代表的なものに鉄鋼メーカーの高炉から排出される高炉スラグがある。もっとも一般的な方法で、どの企業も行っている。2つ目は、CO2を吸収した炭酸カルシウム微粉末を材料として再利用する方法だ。この粉末をコンクリートに混ぜ込むことでコンクリート内にCO2を貯蔵し、見かけ上のCO2を減らすことが出来る。
「2つ目の方法は、CO2を吸収した炭酸カルシウム微粉末の商業化が達成されれば比較的容易であり、流通を含め、利用の仕組みが業界全体でできつつあります。しかしこれだけではCO2の吸収量に限界があることも事実です」(閑田氏)
以上の2つに加えてSUICOMはCO2を直接吸収するという3つ目の手段を有している。この技術を持っているのは現段階では鹿島が唯一だ。建造物の特徴や工期、現場の環境に合わせて、工法のバリエーションを持たせることで効果的にCO2排出量を削減できる。
一方で、SUICOMには経済合理性の担保の面で2つの課題が残っている。1つ目は、CO2吸収時間の短縮だ。現在は30ミリメートルの厚さのSUICOMを完成させるのに2~3週間の吸収時間が必要だが、費用削減や工期短縮のために最短3日が理想的だという。それに向けて改良やCO2を送る環境の整備に取り組んでおり、現段階では1週間~10日に短縮するめどがついている。2つ目は、原料として購入しているCO2の価格だ。現在使用しているCO2は企業が副産物として集めたものを精製して流通しており、工業品としては高価である。
「さらにカーボンニュートラルが進み各企業が集めたCO2が私たちのところへ自動的に集まってくるサイクルができれば理想的ですね」(鹿島建設・取違剛氏)
同社が幹事会社を務めるGI基金事業では30年までに環境配慮型コンクリートで5%のシェアを取り、50年には3割の目標を掲げている。日本では年間約1億立方メートルのコンクリートが使用されており、5%は約500万立方メートル、3割は約3千万立方メートルに相当する。
「30年までの6年間でSUICOM単一で5%のシェアは難しいかもしれませんが、ハイエンドの技術として進化させつつ、現在主流であるセメントを減らしたコンクリートやCCU(CO2を回収・貯蔵)材料の使用量を今まで以上に増やすことでカバーしていきます」(閑田氏)