身の回りには鉄製品があふれているが、中でも一番技術力が問われるのが自動車用鋼板だ。薄くて軽くて強いのはもちろん、加工しやすさを兼ね備えなければならない。そのためこれまでは高炉によってしか生産できないと考えられていた。その常識を東京製鐵が変えた。文・聞き手=関 慎夫(雑誌『経済界』2024年8月号巻頭特集「歴史が動いた! 企業の素材発掘記」より)
電炉鉄のCO2排出量は高炉鉄の5分の1
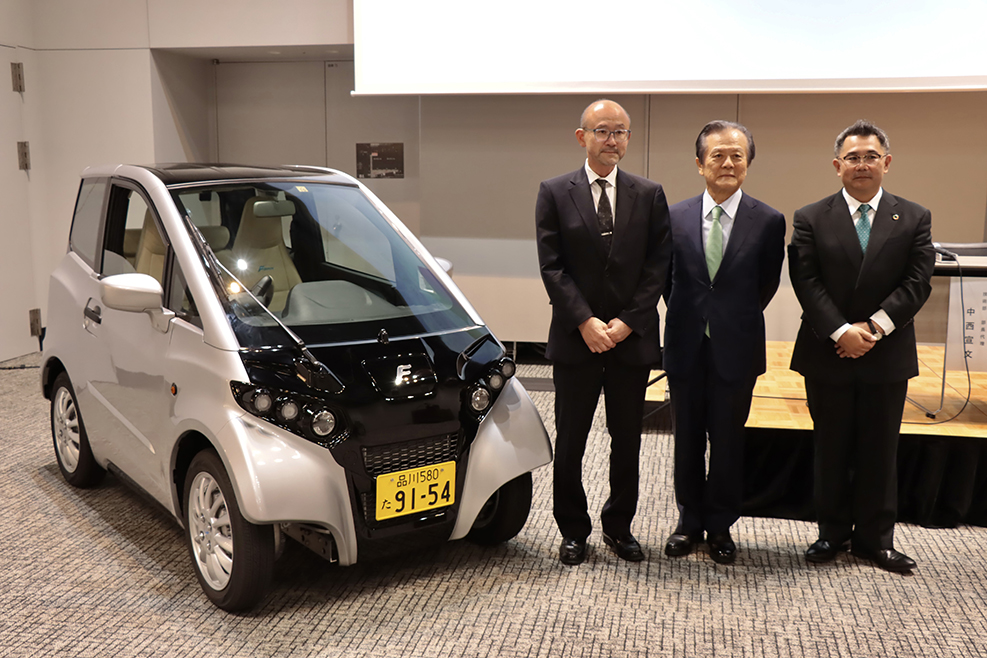
「鉄は国家なり」。かつてよく聞いた言葉だ。元はドイツの宰相・ビスマルクが語ったといわれている。建物をつくるにしても自動車を製造するにしても、土台となるのは鉄。鉄の生産量は、国家の工業力に比例する。
日本でも明治政府の富国強兵スローガンの元、北九州市に官営八幡製鉄所が誕生、以来鉄鋼生産は国の重点施策となった。戦後もそれは引き継がれ、日本は1990年代まで粗鋼生産量世界一だった。日本の高度成長は鉄鋼生産なくしてはあり得なかった。
今後も鉄の重要性は変わらないが、一つ大きな問題点がある。高炉で鉄を生産するには、鉄鉱石を石炭由来のコークスとともに燃焼させる。これにより鉄鉱石に含まれる酸素を分離、コークスの炭素を結びつけて粗鋼となるのだが、この段階で大量のCO2が発生する。1トンの鋼鉄を製造するのに1・8トンものCO2が発生するといわれており、日本の産業界で発生するCO2の40%、日本全体のCO2発生量の17%が鉄鋼業によるものだ。
地球環境を守るためにもCO2削減は喫緊の課題だ。そのため鉄鋼業界でも水素による脱酸素などの取り組みが行われているが、コストの問題もありはかどってはいない。
そこで今、注目を集めているのが電炉によるリサイクル鉄だ。ビルの解体や自動車をスクラップする際、大量の鉄スクラップが生まれる。これを溶融し、鉄製品として再生するのが電炉メーカーだ。電炉はその名の通り、電気によって加熱する。火力発電に由来する電力の場合、発電段階でCO2が発生するが、それでも高炉に比べ、4分の1に抑えることができる。
現在、世界で生産される鉄の70%が鉄鉱石から作られ、残り30%がスクラップ鉄を再生したものだという。循環型社会である「プラチナ社会」を提唱する小宮山宏・三菱総合研究所理事長によれば、「先進国では必要量に匹敵するスクラップ鉄が発生している」という。つまりスクラップ鉄を電炉によって100%再生することができれば高炉は不要となり、CO2排出を抑えることができる。現にビル建設などに使われるH型鋼に関しては、電炉による生産が7割を超えている。
ただし電炉によるリサイクル鉄には弱点がある。鉄は用途に応じてさまざまな成分が添加される。さらには建設廃材などでは、さまざまな不純物が入り込む。これを電炉で完全に除去するのは技術的にもコスト的にも難しい。そのため電炉鉄は高炉鉄より品質が悪い、というのがこれまでの常識だった。
鉄製品の中で、自動車用鋼板は特別な存在だ。自動車の重量を抑えるためには薄くなくてはならず、それでいて強度が必要だ。しかも加工しやすくなければならない。日本が世界一の自動車大国になった背景には、高品質の自動車用鋼板がある。そしてこれまで、この市場は高炉鉄が独占していた。
昨年11月に誕生したスクラップ由来のEV
ところがその常識が覆った。昨年11月、EVベンチャーのFOMM(フォム)が小型EVのコンセプトカーを発表したが、使われていたのが建材スクラップ由来の鋼板だった。これまで自動車鋼板をスクラップした自動車はあったが、建材スクラップはこれが初めてだった。
日本は高炉、電炉を合わせて年間約9千トンの鉄を生産している。その最大の用途が建設資材で約50%。それに次ぐのが自動車用鋼板で約20%。前述のとおり、建設資材のH型鋼ではリサイクル鉄が主力となっているが、自動車用鋼板はほぼ手つかずだった。これを高炉鉄から電炉鉄へと切り替えることができれば、CO2排出量をさらに抑えることができる。
このリサイクル自動車用鋼板をつくったのは、電炉最大手の東京製鐵。社長の奈良暢明氏によれば、プロジェクトがスタートしたのは2021年。自動車用鋼板に必要な強度を得ることに加え、成型のしやすさを得るために試行錯誤し、ようやく要求に応えるレベルの品質を確保した。
奈良社長は社内で「不純物と言うな」と言い続けている。前述のように鉄スクラップには鉄以外の合金元素成分が多く含まれている。かといってこれを取り除こうとすればコストがかかり、リサイクルの意味がなくなる。
そこで東京製鐵では不純物を不純物と捉えず、含まれた成分の特性を生かした電炉鉄ができないかと考え続けてきたという。例えば銅を含むスクラップ鉄なら、銅の錆びにくい特徴を生かし、海辺の構造物用の鉄をつくるといった具合だ。このような発想の転換があったからこそ、高炉でしか製造できないと思われていた自動車用鋼板を電炉でつくることに成功した。
今後、東京製鐵は25年の量産を見込む。今、自動車業界は「100年に一度の変革期」(豊田章男・トヨタ自動車会長)を迎えている。EV化、自動運転など、新しい波が押し寄せている。それと同時に、クルマを形づくる素材にも大きな変革が訪れようとしている。
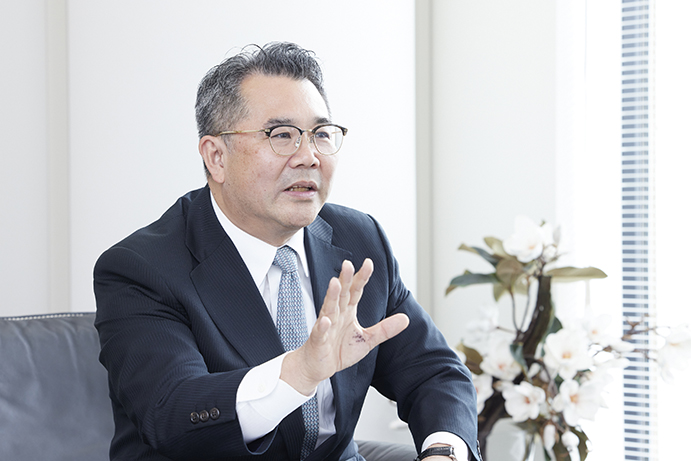
なら・のぶあき 1970年生まれ。93年京都大学文学部を卒業し東京製鐵入社。2012年取締役総務部長、21年取締役常務執行役員を経て23年6月社長に就任。
社内では「不純物と言うな」と言い続けている
―― 電炉によって生産した鉄は、鉄スクラップの再生のため、安いけれど低品質というイメージがありました。それが自動車用鋼板を目指すまでに進化したのですね。
奈良 そこに至るまでの経緯を少し説明させてください。私が東京製鐵に入社したのは1993年ですが、その直後に、それまでの拡大路線がバブル崩壊によりつまずき、赤字に転落した。転機になったのは、日本の鉄スクラップが需要を上回るようになってきたことです。それまでは海外から輸入していたものが、国内自給率が100%を超え、今では2割以上を輸出しています。そのため原料を廉価に調達できるようになり、競争力がついてきた。もう一つは低炭素化の進展です。電炉は高炉に比べてCO2排出量は4分の1ですみます。それにより電炉が再評価されるようになってきました。
電炉で生産した鉄の主たる用途は建設用資材です。東京製鐵では私が入社する前から鋼板の生産に取り組んできましたが、顧客の要望レベルが非常に高い。日本国内には電炉メーカーは30社以上ありますが、鋼板をつくっているのは3社にすぎません。しかも自動車部品を作る時に生じたような品位の高い加工スクラップを原料にすることが多い。その点われわれはヘビースクラップと言われるビルの解体などで生じるスクラップから生産しています。ヘビースクラップは鉄スクラップの7割を占めます。量が多いから廉価ですが、鉄以外の合金元素を多く含むため品質を高めるのが難しい。それでも東京製鐵では、元の原料よりも高品質な鉄を提供する。これがわれわれの歴史であり信念です。
―― 不純物を取り除くのは難しいのではないですか。
奈良 確かに難しいのですが、われわれはそうは考えません。鉄の強度を増すためには、マンガンなどの元素を添加します。発想を変えれば、既に硬くする原料が入っていると考え、この特性を生かした製品をつくろうとなるわけです。銅が入っているなら錆びにくい特性を生かし、取り切れないのであれば、入っている成分をそのまま活用する。ですからスクラップ鉄の成分を調べ、それに基づいたレシピを作成、さらに成分を配合するなどして目的に合った鋼板をつくる。これを過去30年間にわたりやってきました。
ですから社内では、「不純物と言うな」と言っています。すべてが重要な構成要素です。やりかたによってはいかようにも使うことができると考えて言います。
―― 自動車用鋼板をなぜつくろうと考えたのですか。
奈良 日本では毎年3千万トン以上の鉄スクラップが出てきますが、国内で消費しきれず700万トンほどを輸出しています。これを国内で消費するには、建設資材だけでなく、他の用途を探す必要があります。そこで当社が鋼板生産を始めて30年が経った2021年からプロジェクトをスタートしました。自動車用鋼板は非常に高い品質レベルが必要です。それをヘビースクラップから生産する。そこにチャレンジすることでイノベーションを起こしたい。そう考えたわけです。
そこで協力相手を探していたら、FOMMの鶴巻日出夫社長がわれわれの考えに共感してくださり、ぜひコンセプトカーを一緒につくりましょうということになりました。
自動車用鋼板は薄さや硬さ、加工しやすさがなければなりませんが、最初のチャレンジでは硬さが足りなかった。2度目の挑戦では硬さは十分だったものの、硬くなりすぎて加工が難しい。3度目のチャレンジでようやく、硬さと加工しやすさを両立させることができました。
こうした取り組みを通じて電炉鋼板が広く使われるようになれば、CO2削減にも役立ちます。量産化することができれば、鉄スクラップが原料なのでコスト的にも成り立ちます。ですから非常に大きな可能性を秘めていると思います。