NEXT Logistics Japan(以下NLJ)は2018年に設立、アサヒグループホールディングスをはじめ業種業態を超えた20社が参画。25メートルダブル連結トラックの運用や世界初の量子コンピューターを使ったシステムを駆使し、物流業界の変革に挑む。梅村幸生社長にその取り組みと成果を聞いた。聞き手=萩原梨湖 Photo=横溝 敦(雑誌『経済界』2023年7月号巻頭特集「物流クライシス2024」より)
梅村幸生・NEXT Logistics Japan社長のプロフィール
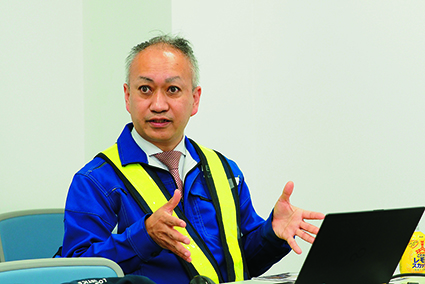
うめむら・ゆきお 慶應義塾大学総合政策学部卒。1996年日野自動車入社。マーケティング、商品企画、宣伝プロモーションを主に担当しトヨタ自動車総合企画部出向。日野自動車新事業企画部長を経て2018年6月NEXT Logistics Japan設立、社長に就任。
ダブル連結トラック導入で「稼働率×積載率」を最大化
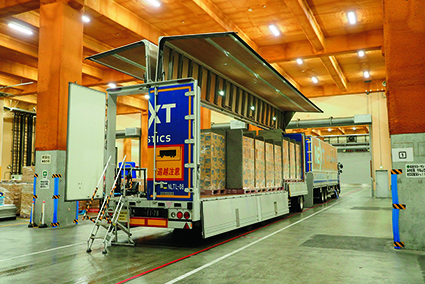
―― NLJは設立の目的として、ドライバー不足、カーボンニュートラル、ホワイト物流の構築といった物流の社会課題解決を掲げています。
梅村 このプロジェクトはトヨタグループのメンバーが集まり、われわれが持つ新しい技術を使って社会課題の解決に何ができるかという議論から生まれました。私は日野自動車出身で、構想段階からこの事業に携わってきました。
自動車業界ではCASE(Connected=コネクテッド、Autonomous=自動運転、Shared=シェアリング、Electric=電気自動車)の実現を目指し、活動を行っています。
しかし、今すぐにトラック業界で自動運転や電動化が実現できるわけではありません。
その一方で物流業界の課題の一つであるドライバー不足は、「物流2024年問題」に直結する深刻な問題です。現在、低給与、長時間労働などの問題でドライバーのなり手が減少しており、高齢化が進んでいます。残業が規制され稼げない業界になるとドライバー職の人気はさらに落ち、新規参入者は減る一方、ドライバー不足はさらに加速します。
自動運転や電動化が実現するまで、ただ待っているだけでは日本のあらゆるサプライチェーンが成り立たなくなり、経済の根幹が崩れてしまいます。
―― ドライバー不足と言われる「物流2024年問題」まで残り1年です。
梅村 われわれが目指したのは、1人のドライバーが運べる量を増やし、生産性を上げることです。
そのために当社では25メートルダブル連結トラックを導入し、荷物の混載輸送を始めました。ダブル連結トラックとは、運転席がある大型トラクタの後ろにもう一つトレーラーを付けたもので、大型トラック2台分の荷物を運ぶことができます。
そこに各企業の荷物を混合で積載するため、積載率も併せて向上させることができます。
当社では複合積載率を計算し、1トラックごとの生産性を評価しています。複合積載率とは、1つのトラックに積載可能な容積の比率と、積載可能な重量の比率を足して2で割ったものを指します。
われわれのダブル連結トラックの平均複合積載率は63%、最大値は89%です。
それに対して日本のトラック全体の積載率は約4割程度と非常に低く、平均6割は空気を運んでいることになります。
なぜこのような低い積載率になるかというと、1日24時間の稼働時間でみると満載、半分、空車などさまざまな状態で走行していることが分かります。また、荷物によって月間や年間で物流の閑散期と繁忙期があるからです。委託されている物流業者はこれに合わせてトラックで運んでいますが、うまく管理できずにいます。
一方で当社はというと、25メートルダブル連結トラックの混載に加え、すべての輸送をダイヤグラムにあてはめて定時に運行しています。
そのため、当社の物流センターがある相模原から西宮間の長距離輸送でも、中間地点にドライバーチェンジ拠点を構えることで稼働率100%に近い状態での運行が可能となり、積載率と相まって効率化の最大の効果を得ることができています。
―― 1台のトラックで運べる荷物の量が増えると排出するCO2の量も削減できますね。
梅村 グローバルな企業にとって、カーボンニュートラルは非常に重要な課題です。サプライチェーンにおけるCO2排出量の削減方法として、どの企業もCO2が出ない生産設備への投資や、グリーン電力の購入に目が向きがちですが、物流の効率化はもっと簡単です。オペレーションの変更だけで済むため、明日からでも取り組むことができます。
世界初のシステムを自社開発積み付け・割付を40秒で計算
―― 多種多様な荷物を大型トラック2台分に積み込むのは、積み方や順序を決めるのに時間がかかるのではないですか。
梅村 人が割り付けるのは時間がかかりすぎてしまうため、NeLOSS(ネロス)という、配車と積み付けの組み合わせ計算、両方を同時に行うシステムを開発しました。
NeLOSSは量子コンピューターを使ったソフトで、これまではベテランの人間が割付と積み付けの組み合わせを考え、積み込みが終わるまで、2時間以上要していました。しかし、NeLOSSが配車と組み合わせ計算の最適解を40秒で導いてくれるため、残りの作業は指示通りフォークリフトで荷物を積み込むだけになります。
われわれの取り扱う荷物はすべて、高さ、長さ、幅、重さなど荷姿がバラバラです。匂いを発するシャンプーやカップ麺は、匂いを吸着しやすいものと混載することはできませんし、重い物同士を混載してしまうと規定重量を超過してしまいます。荷室内の重さの配置に配慮しないと車体のバランスが取れません。これらを考慮し最適な組み合わせを自動で計算するのがNeLOSSです。
現在は関東〜関西間の配車と積み付けを行っていますが、今後は日本全国に広げていく予定です。
―― 一気に効率化が進みますね。
梅村 さらに、各企業の変動する物流に対応する方法としては、当社で取り扱った荷物をデータ化し、その傾向を分析しています。現段階でパレット22万枚分のデータを蓄積しています。
このデータに基づき各企業からの輸送オーダーを予測し、毎日の予実管理までを行っています。実際に予測通りのオーダーが入ったかどうか、PDCAサイクルを回すことで予測の精度をさらに向上させる構想です。
また、効率化を見える化するため、予実管理の結果を荷主と共有しています。例えば、積載率の目標として70%という基準があるのですが、急遽どこかの企業が輸送をキャンセルすると、積載率はその分減ってしまいます。急なキャンセルで非効率になった部分が一目瞭然なので、物流の効率化に対する意識を高めることができています。
将来的には、最適なダイヤグラムやルートの計算機能も実装し、割付・積み付けに限らず全業務で活用できるようバージョンアップさせていきたいです。